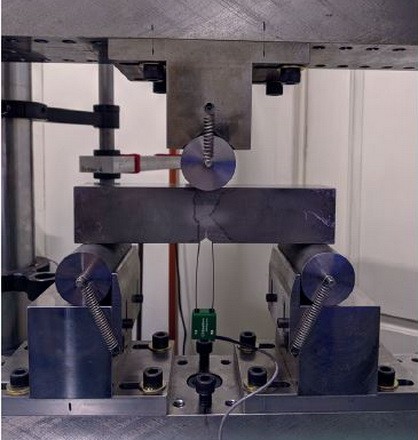
The challenge of separating steel welds with acceptable flaws and tolerances from those that are unacceptable (defects) is nearly as old as the challenge of welding itself. This challenge will continue to be with us long into the future. Setting limits that are too stringent can cause economic waste and may even create unanticipated new technical risks when unnecessary modifications are made. Alternatively, setting limits that are too loose increases the risk of fracture.
Across the many industries that use welded joints, there are two different strategies for judging inspection results when addressing this challenge. The first strategy is to use a consensus-based, standardized, codified set of criteria, often referred to as workmanship criteria. In AWS D1.1/ D1.1M:2020, Structural Welding Code — Steel, Clauses 7 and 8 exemplify this approach. The second strategy is to formulate project-specific acceptance criteria, usually through a combination of fracture mechanics, metallurgy, and performance-based inspection criteria. The strategy goes by many names, including alternate flaw acceptance criteria, engineering critical assessment, damage-tolerant design, fit-for-purpose assessment, fit-for-service assessment, and performance-based design.
In this article, engineers and welding experts Steven Altstadt and Robert Warke discuss the benefits of employing an optional strategy to evaluate flaws when welding to AWS D1.1.
This article originally appeared in the July 2020 issue of Welding Journal. The image is courtesy of Product Evaluation Systems Inc.
RELATED INFORMATION
-
WJE metallurgical and welding consulting engineers have extensive experience in the... MORE >Services | Metallurgical Consulting
-
Robert W. Warke, Associate PrincipalWJE Northbrook MORE >People | Robert W. Warke, Associate Principal
-
Our metallurgical and applied mechanics engineers provide solutions related to design... MORE >Services | Metallurgy and Applied Mechanics
-
We provide dedicated engineering support and specialized testing services for all sectors across... MORE >Markets | Energy