WJE PROJECTS
Pressure Vessel Design Rerates
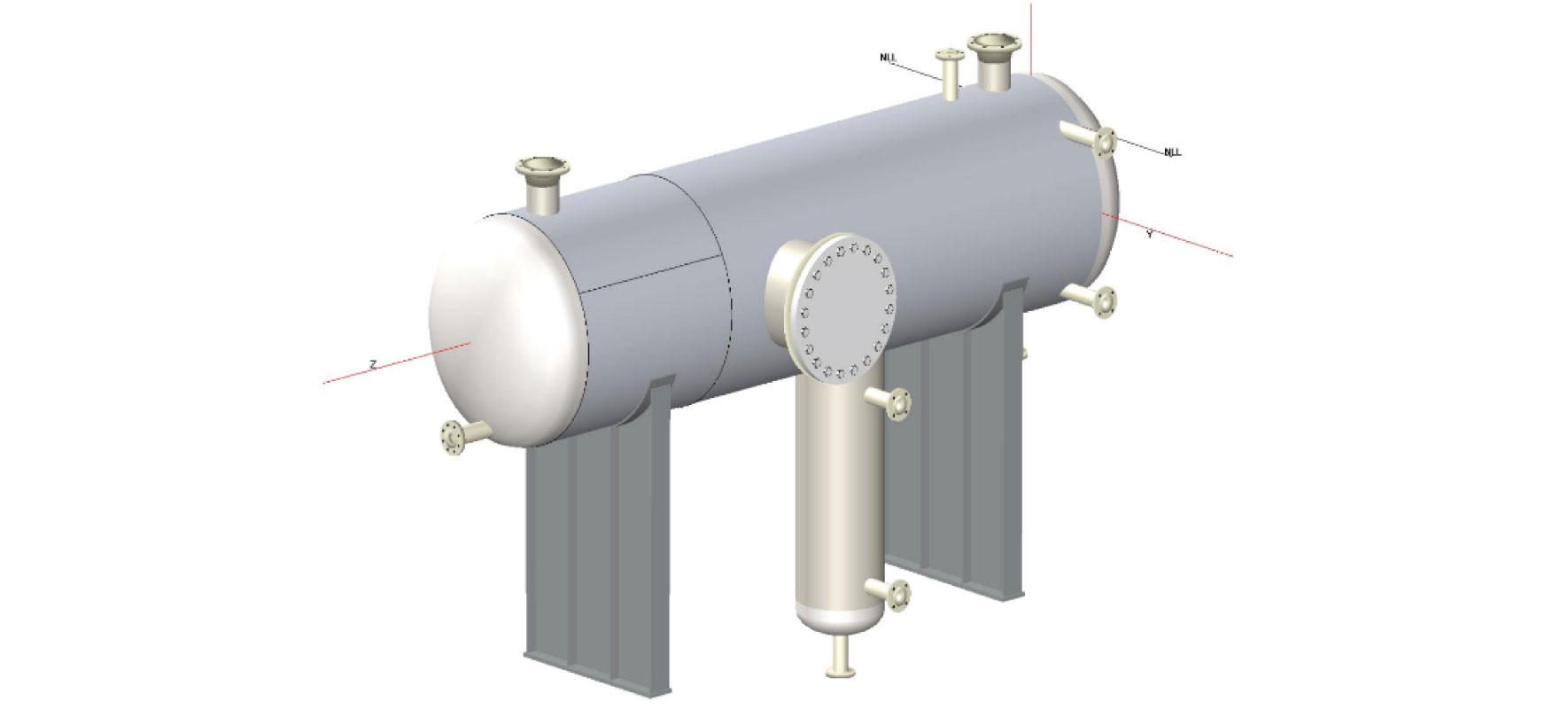
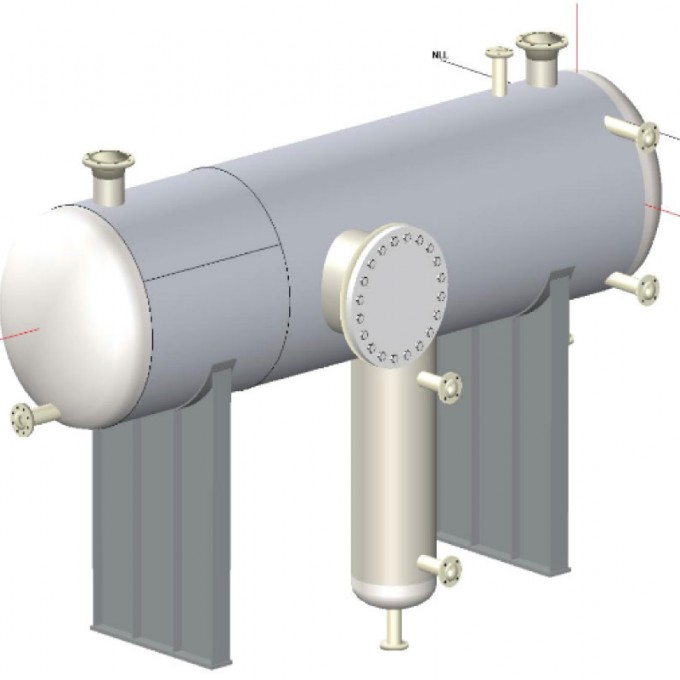
CLIENT |
Confidential |
LOCATION |
Midwest, United States |
Design Calculations to Support NBIC Alterations
WJE was asked to perform design calculations according to ASME Boiler and Pressure Vessel code requirements to support rerating several vessels to higher maximum allowable working pressures (MAWP) and/or maximum allowable working temperatures (MAWT). The objective of the effort was to support National Board of Inspection Code (NBIC) alterations by the Owner/Operator by verifying the suitability of the vessels to operate at design conditions outside those listed on the nameplates, and establish applicable corrosion allowances.
BACKGROUND
In order to optimize process flow through a facility, an owner/operator may need to alter the design conditions for a given vessel to expand the operating envelope. This rerating can be a useful tool to debottleneck, change throughput, and address changes in service for pressurized equipment. National Board Inspection Code (NBIC) Part 3 provides guidance to perform, verify, and document acceptable alterations, including rerates, to pressure-retaining items regardless of the Code of construction.
SOLUTION
WJE performed ASME code calculations with the commercial pressure vessel software COMPRESS® to verify the acceptability of the requested rerate design conditions. In each case, allowable stress values for each component were defined based on the original construction code as a function of the design temperature. The most recent API 510 inspection reports were reviewed to establish the current expected condition of each vessel.
The calculations considered all applicable loading, including MAWP, MAWT, full vacuum pressure, dead loads (e.g., insulation, appurtenances, etc.), and hydrostatic loading from the contents. For some vessels, wind, seismic, and nozzle loading were also addressed.
For each vessel, a comprehensive engineering design calculation report was produced for review by the Owner/Operator’s designated Authorized Inspector. The report included maximum allowable corrosion allowances for each component to establish inspection interval frequencies.
RELATED INFORMATION
-
We provide dedicated engineering support and specialized testing services for all sectors across... MORE >Markets | Energy
-
Our metallurgical and applied mechanics engineers provide solutions related to design... MORE >Services | Metallurgy and Applied Mechanics
-
WJE fracture mechanics consultants have provided fracture mechanics assessment and fitness for... MORE >Services | Fracture Mechanics Assessment and Fitness for Service