WJE PROJECTS
Flare Knockout Drum
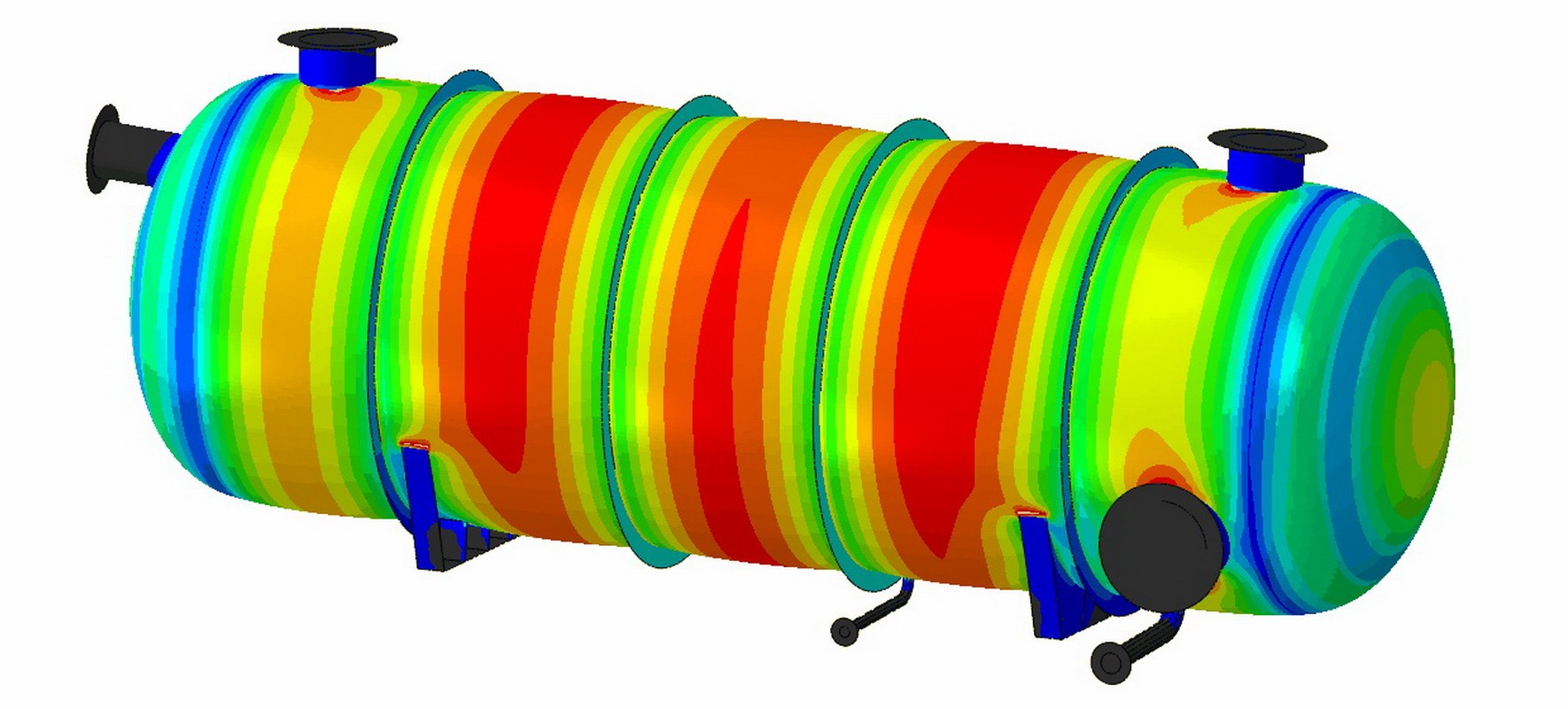
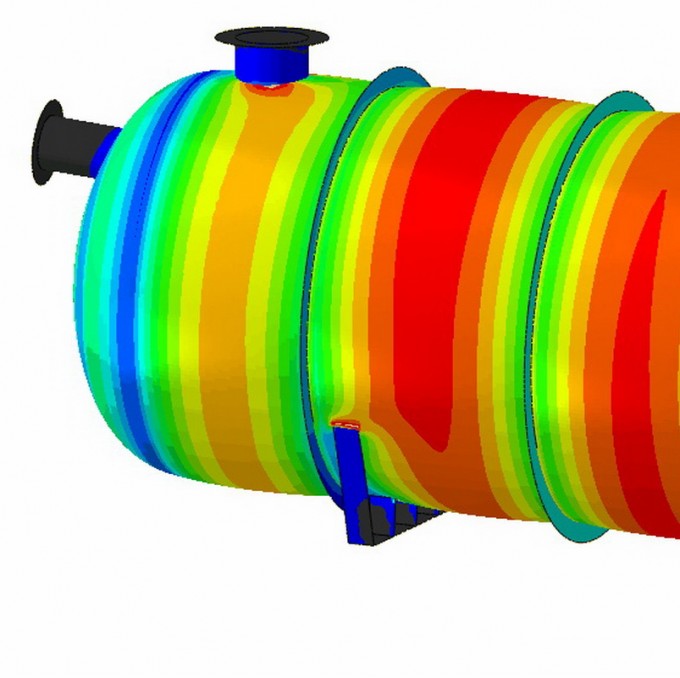
CLIENT |
Confidential |
LOCATION |
Midwest, United States |
API 579-1 Fitness for Service Assessment of Local Thinning
WJE was asked to perform a fitness for service (FFS) assessment to evaluate local thinning and metal loss in the shell of a Flare Knockout (KO) Drum. The damage mechanism was related to leakage of an external steam jacket installed on the vessel and characterized with phased-array ultrasonic testing (PAUT) scans of the vessel to measure remaining wall thickness. The objective of the effort was to evaluate the in-service damage to establish that the vessel design was safe to operate and establish the remaining life of the drum.
BACKGROUND
The Flare Knockout Drum is used for bulk separation of gas and liquid phases of a product stream, where the recovered liquid or condensate is collected at the bottom of the vessel, and the vapor is burned in the flare system. The drum was constructed according to ASME Boiler and Pressure Vessel Code Section VIII, Division 1. The 7-foot-6-inch Outer Diameter (OD) by 19-foot-9-inch-long vessel was constructed from SA-516 Grade 70 carbon steel, with a nominal shell thickness of 0.375 inch and a corrosion allowance of 0.125 inch. The vessel design includes saddle supports, internal baffles, vacuum rings, and a variety of nozzles.
SOLUTION
WJE performed an FFS evaluation based on API 579-1/ASME FFS-1 to determine whether the Flare KO Drum was safe to continue operating using Part 4, Assessment of General Metal Loss, and Part 5, Assessment of Local Metal Loss. The assessment used Level 3 methods based on the proximity to and interaction of the local thin area with structural discontinuities, including stiffening rings, nozzles, and saddle supports.
To establish protection against global plastic collapse and other relevant failure mechanisms, a nonlinear elastic-plastic finite element (FE) model of the drum was created with representative geometry, boundary conditions, and design loading. The model incorporated remaining wall thickness readings from the PAUT inspection by mapping the high-fidelity grid-style measurements directly onto the FE mesh to capture the as-inspected state of the vessel. To address the remaining life and establish inspection intervals, iterative analyses were performed to identify a future corrosion allowance based on short- and long-term corrosion rates for the drum.
Based on the applicable design loading and acceptance criteria listed in API 579-1, the FFS evaluation demonstrated that the Flare KO Drum had sufficient remaining strength to satisfy the minimum required design margins for in-service equipment and was fit for continued service with periodic monitoring.
RELATED INFORMATION
-
We provide dedicated engineering support and specialized testing services for all sectors across... MORE >Markets | Energy
-
Our metallurgical and applied mechanics engineers provide solutions related to design... MORE >Services | Metallurgy and Applied Mechanics
-
WJE fracture mechanics consultants have provided fracture mechanics assessment and fitness for... MORE >Services | Fracture Mechanics Assessment and Fitness for Service