WJE PROJECTS
CSX Bridge QDC 1.71
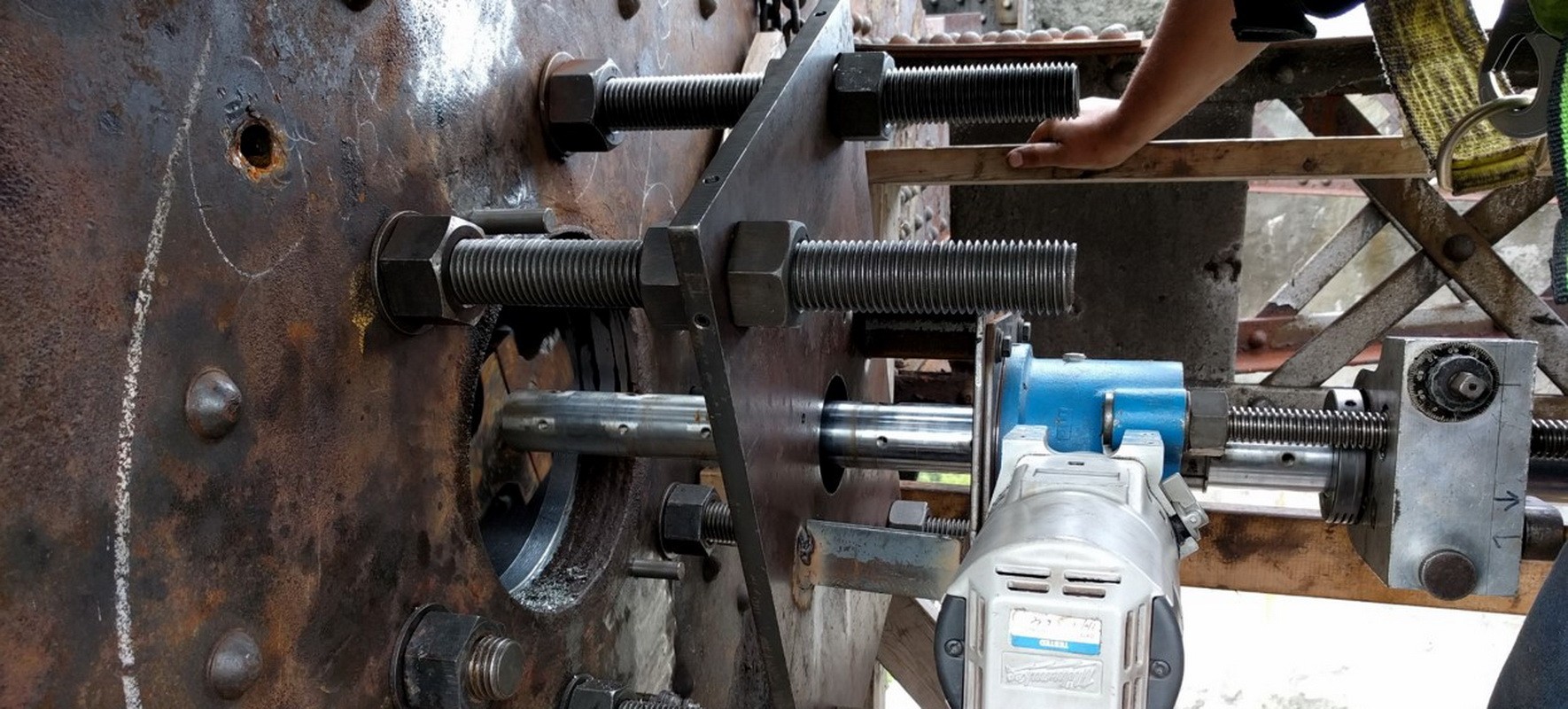
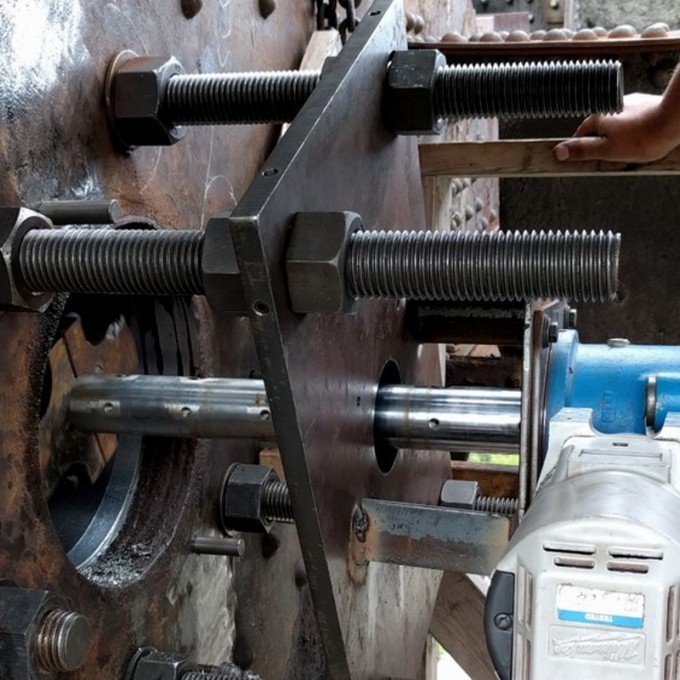
CLIENT |
CSX Transportation |
LOCATION |
Buffalo, NY |
Emergency Response, Inspection, and Mechanical Design
WJE provided an emergency response to investigate an issue affecting operation of the bridge. The north rack and pinion teeth were “skipping” which prevented the movable span from opening. While WJE was able to diagnose the cause of the skipping and quickly implement a temporary repair to resolve that issue, a limited mechanical inspection identified that the north counterweight trunnion was in poor to critical condition due to severe wear at the span to pin connection, fractured sleeve retaining bolts, and misaligned lubrication ports.
BACKGROUND
Completed in 1912, CSX Bridge QDC 1.71 is a double track Strauss heel trunnion bascule bridge in Buffalo, NY. The structure spans over the Buffalo River and is operated infrequently for marine traffic. The span is operated mostly in the winter months to permit ice breaking operations on the Buffalo River in an effort to prevent ice jams and resultant flooding in the South Buffalo communities along the river. The waterway is considered a federal navigation channel and is controlled by both the Coast Guard and the Army Corps of Engineers. Presently CSX operates a single track over the structure. QDC 1.71 is a critical link in the CSX system.
SOLUTION
WJE provided all required mechanical engineering services, including inspection, evaluation of repair options, preparation of plans, specifications and cost estimates, and construction services for the rehabilitation of the counterweight trunnion bearing.
The rehabilitation included a unique jacking system that used the structure as the support for the counterweight truss thereby eliminating the need for a costly and time-consuming temporary foundation. After the span was jacked, the bearing repair consisted of securing the truss to the existing pin, removal of the sleeve bolts, installation of temporary sleeve bolts, removal of the existing pin, replacement of the existing bearing bushing with modifications to facilitate assembly, field machining to restore fits between the pin and both the structure and the sleeve, installation of a new pin with proper fits, and installation of high-strength studs and dowels to prevent relative movement between the structure and the bearing assembly.
All work was completed during a limited river closure with little disruption to rail operations.
RELATED INFORMATION
-
Our knowledge of bridge performance is supported by technical expertise in structural... MORE >Services | Bridge Engineering
-
We are an industry leader in the design, inspection, and repair of heavy movable structures MORE >Services | Heavy Movable Structures
-
We engage a full suite of state-of-the-art instrumentation and monitoring capabilities to test... MORE >Services | Instrumentation and Monitoring
-
Learn about our Doylestown office MORE >Offices | Doylestown