WJE PROJECTS
John Marshall Hotel
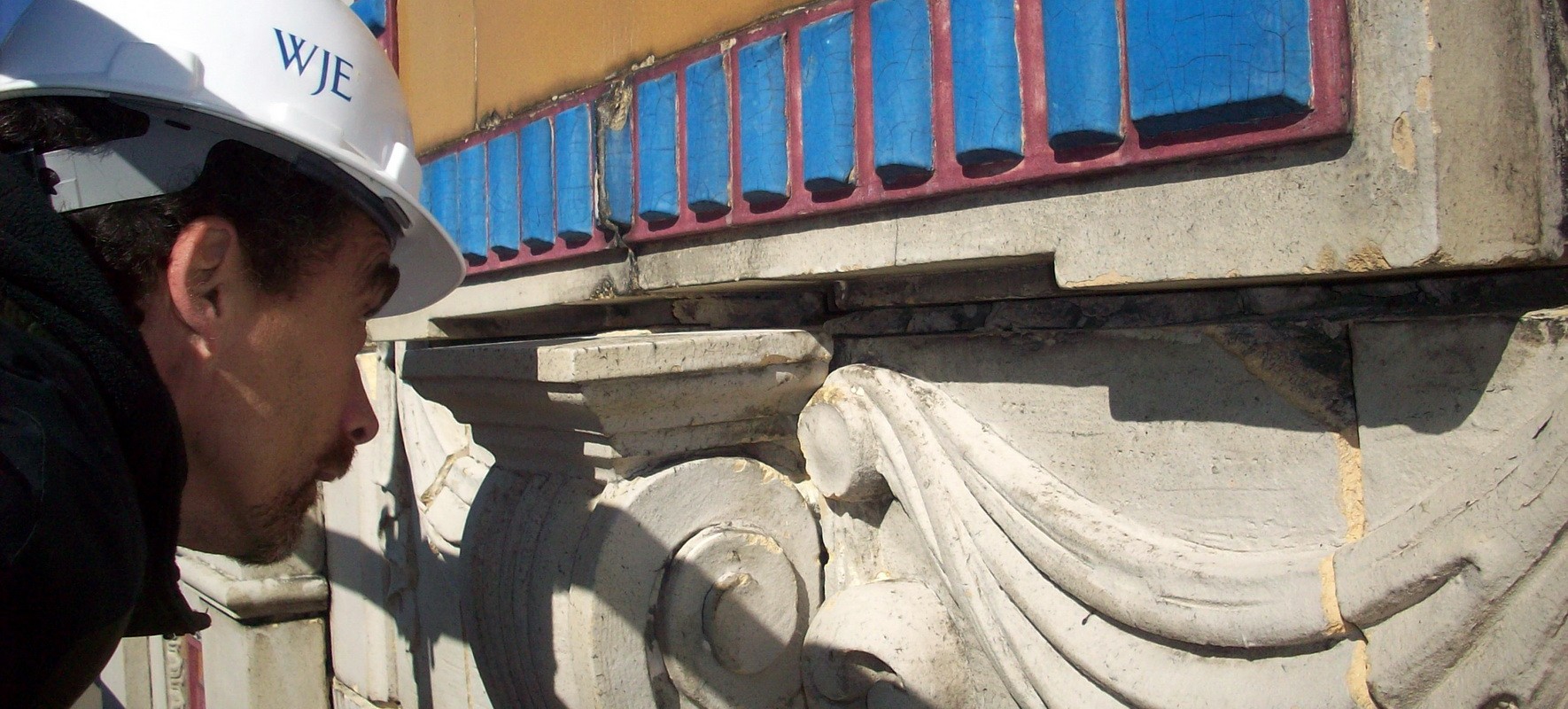
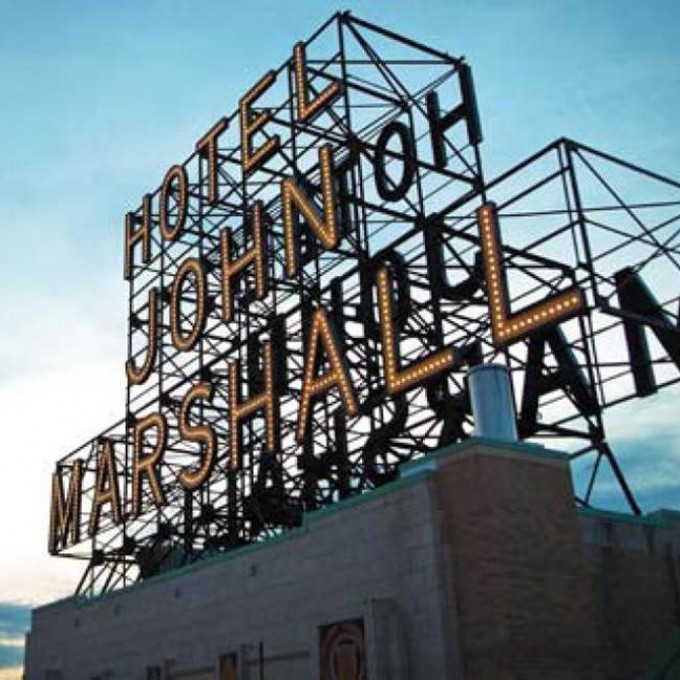
CLIENT |
Mid-Continental Restoration |
LOCATION |
Richmond, VA |
Limestone and Terra Cotta Repairs as Part of Adaptive Reuse
In 2008, plans to convert the space into apartments were temporarily derailed when two limestone cladding panels fell from above the main entrance onto the sidewalk below. Another engineering firm was initially engaged to replace the failed panels and to stabilize and develop repairs for the other panels, but it became clear that the repair design was going to significantly impact the interior of the building as well as the overall project cost. The project team came to WJE in hopes of developing a more cost-effective and schedule-friendly approach.
BACKGROUND
Completed just prior to the Great Depression as the Grand Old Southern Hotel, the structure is fifteen floors in height and roughly C-shaped in plan. The steel structural frame is clad with composite mass walls consisting of limestone from the street level through the fourth floor, brick with vertical piers of limestone, and polychromatic decorative terra cotta insets from the 5th through 14th floors. The hotel remained a highly sought after establishment through most of the 20th century; however, urban blight and the construction of more modern and luxurious accommodations eventually impacted the hotel, which booked its last guest in 1988 before going to public auction.
SOLUTION
Through WJE's inspection of the failed area, it was determined that the panel failures were a result of the accumulated load of the limestone cladding combined with accumulation (and confinement) of corrosion scale, which caused the panels to displace outward until the bearing stresses at the kerfs were high enough to fail the stone panels.
The originally proposed limestone panel repair design posed scheduling challenges within a tight construction timeline and failed to meet historic tax credit criteria. Rather than installing bolts through the limestone and terra cotta back-up and into steel framing at the interior, the final repair approach reintegrated the limestone and the terra cotta back-up from only the exterior, using adhesive anchors to secure the limestone to the terra cotta back-up, which maintained the original load path and minimized the need for supplemental strengthening of systems that were not originally designed to carry limestone cladding loads. Through-face adhesive anchors were designed based on test data and load analysis and were used at virtually all limestone panel configurations due to the potential that the existing anchors were corroded and no longer functioning. Every limestone panel was stabilized from the exterior with no need to perform work at the interior, allowing the interior restoration efforts to go forward unimpeded. Additional repairs included full restoration of the polychromatic terra cotta and replacement of unstable brick masonry.
RELATED INFORMATION
-
Clients turn to us when they need a firm that fully understands the aesthetic and functional... MORE >Services | Building Enclosures
-
Our professionals balance the need to provide practical, long-term solutions with the ability to... MORE >Services | Historic Preservation
-
Our professionals deliver practical repair and rehabilitation services that maximize the... MORE >Services | Repair and Rehabilitation