WJE PROJECTS
John Anson Ford Amphitheatre
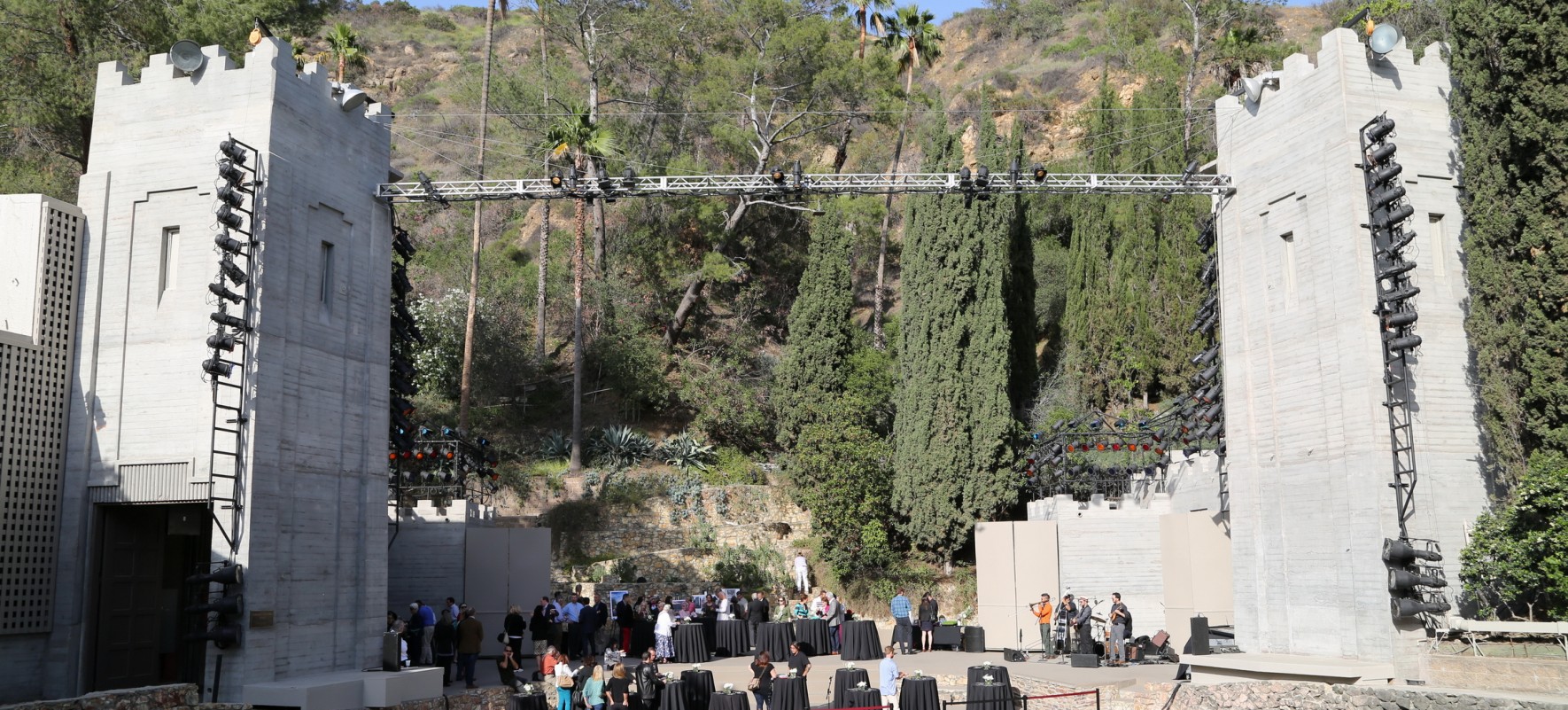
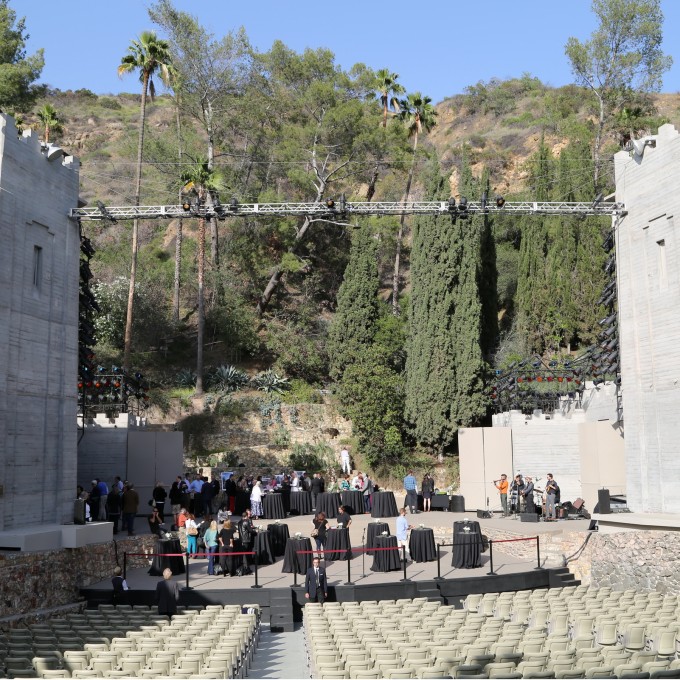
CLIENT |
Levin & Associates Architects for the Los Angeles County |
LOCATION |
Hollywood, CA |
Exterior Envelope, Historic Concrete Repair, and Waterproofing Consulting
Over the last several decades, water intrusion was an ongoing problem at the Ford, in part due to long-deferred maintenance and deteriorated concrete. The original concrete architectural elements had been painted several times. WJE was retained to assist design architect Levin & Associates with the multi-year restoration of the amphitheater.
BACKGROUND
Originally built in 1920, the 1,200-seat outdoor amphitheater was rebuilt and reopened on the same site in 1931. The rebuilt theatre was constructed of cast-in-place reinforced concrete, and the major architectural elements were designed to resemble the gates of Jerusalem. In 1976, the performance venue was named the John Anson Ford Theatre in honor of a Los Angeles County Supervisor who was a great supporter of the arts. Living cypress trees and chaparral shrubs are held in place with a series of retaining walls and form the back "wall" of the concrete stage. It is one of the oldest in-use performing arts venues in Los Angeles.
SOLUTION
To repair the exterior historic concrete walls of the stage structures, the existing coating was removed and the historic concrete was repaired with custom pre-bagged repair material developed to match the original concrete. To match the range of original concrete composition, two different custom mixes were selected.
Especially challenging was consideration of whether to recoat the historic concrete. Although pigmented, film-forming coatings had been applied in the past, once the existing coatings were removed, the varied appearance of the original concrete was appreciated. At the request of the client, WJE evaluated and considered a range of coating systems and provided a comparative assessment of all options—including the option of leaving the original concrete exposed after cleaning. This option, the most desirable with respect to the Secretary of the Interior's Standards for the Treatment of Historic Properties, was found to be viable after successful implementation of concrete repair mock-ups and was eventually selected by the project team.
The coating removal and concrete repair mock-up process took place over a period of two months. After several repair approaches were evaluated, four different coating removal systems and six different concrete repair materials were evaluated. Repairs were then implemented using knowledge gained through the extensive mock-ups.
RELATED INFORMATION
-
We offer in-house expertise for a full range of investigation, analysis, and design services... MORE >Services | Architectural Finishes and Materials
-
Clients turn to us when they need a firm that fully understands the aesthetic and functional... MORE >Services | Building Enclosures
-
Owners and contractors rely on our specialized construction knowledge to properly detail and... MORE >Services | Construction Engineering