WJE PROJECTS
135 Bishopsgate
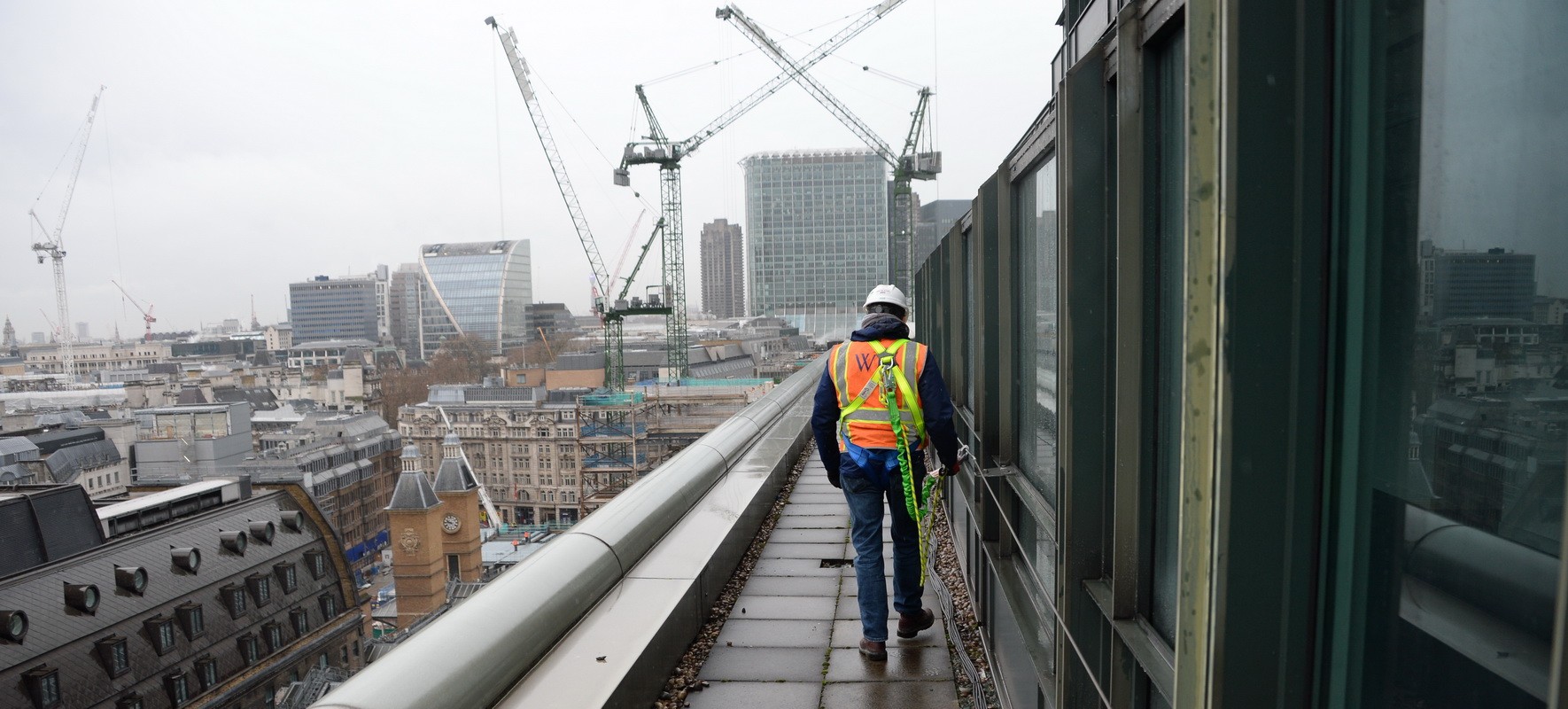
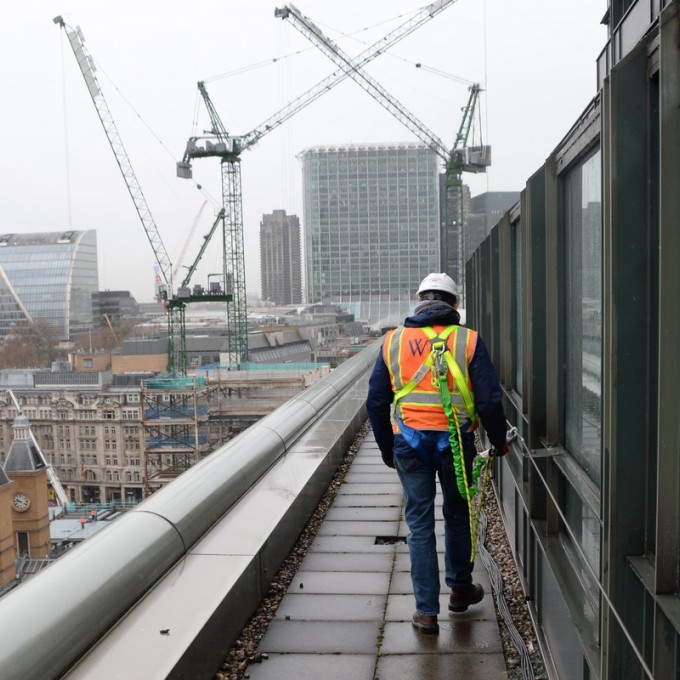
CLIENT |
British Land |
LOCATION |
London, United Kingdom |
Building Enclosure Condition Assessment and Restoration
WJE was retained by British Land to perform an on-site survey and assessment of the above-grade building envelope at 135 Bishopsgate, located adjacent to Liverpool Street Station and Broadgate Estate in the City of London. The purpose of the survey was to work closely with Sir Robert McAlpine on its ongoing refurbishment of the property to develop a technically sound and cost-effective approach to in situ repair, restoration, and replacement of the existing roof, exterior wall, and sloped glazing systems and assemblies.
BACKGROUND
Designed by Skidmore, Owings & Merrill and constructed in 1987, Bishopsgate is a mixed-use office and retail complex with 135 Bishopsgate anchoring the south end of the property. The exterior cladding consists of polished and honed granite veneer panels anchored off-site to a prefabricated steel strong-back frame with field-installed glazed aluminum windows set into punched openings between each panel. The remaining fenestration consists of glazed aluminum storefront and window wall with painted aluminum exterior cladding. The roofing consists of a ballasted, protected membrane roof with precast concrete pavers and washed river rock over rigid insulation and reinforced liquid applied polyurethane membrane.
SOLUTION
WJE performed a close-range survey and assessment of representative sections of the above-grade exterior wall and roof systems and assemblies in support of the ongoing cleaning and refurbishment. Material samples were removed during the survey for laboratory analysis. In addition, WJE performed mock-up in situ cleaning studies to identify the most responsive method of cleaning for the stone veneer, painted metal framing, spandrel panels, and glass surfaces.
Field testing for water penetration resistance was performed at representative locations throughout the property. Flood testing and hose testing were both successful in recreating leaks at observed water staining locations. Infrared thermography was applied informally to gain a general understanding of the potential thermal bridging and air leakage at the exterior wall assemblies. Inspection openings were also made at the roof level to observe concealed conditions.
WJE surveyed interior spaces of the property for evidence of bulk rainwater penetration, condensation, and air leakage. In addition, WJE surveyed the installed inverted roof membrane assembly and associated perimeter flashing, joint sealant, and mastic at representative locations on the outdoor roof areas. The results from this survey were used to develop a range of recommendations for light refurbishment, routine maintenance, and repair.
RELATED INFORMATION
-
We offer in-house expertise for a full range of investigation, analysis, and design services... MORE >Services | Architectural Finishes and Materials
-
We utilize experienced professionals and state-of-the-art modeling and analysis techniques to... MORE >Services | Building Enclosure Testing
-
Clients turn to us when they need a firm that fully understands the aesthetic and functional... MORE >Services | Building Enclosures