WJE PROJECTS
Amoco Building (Aon Center)
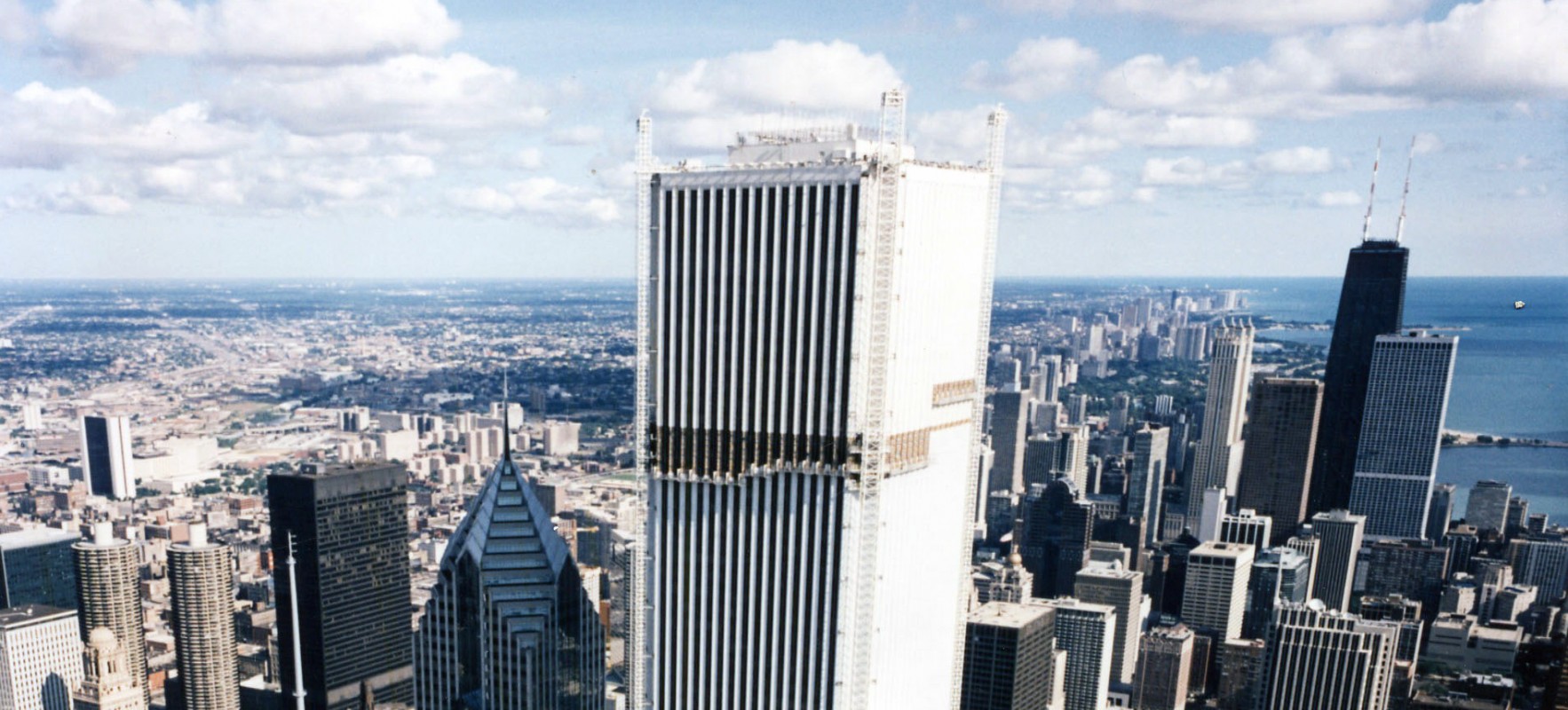
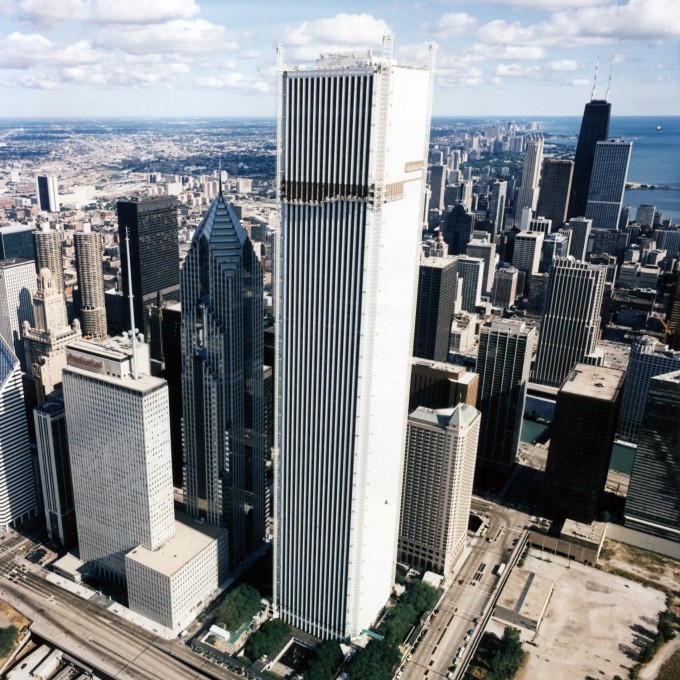
CLIENT |
Amoco Properties, Inc. |
LOCATION |
Chicago, IL |
Distressed Marble Panel Investigation and Granite Reclad Design
After routine inspection of the building's facade revealed cracking and bowing of the marble panels, Amoco sought an expert to investigate the nature and extent of the damage and to develop solutions to restore the facade's structural and aesthetic integrity.
BACKGROUND
Completed in 1973, the eighty-three-story Amoco Building is a dominant feature of Chicago's skyline. Fortified by a tubular steel frame and originally clad with 44,000 panels of 1 1/4-inch-thick white Italian Carrara marble, the skyscraper was a structural feat, setting the record for the world's tallest marble-clad building.
SOLUTION
WJE determined that exposure to cyclic temperatures caused the thin marble panels to expand and contract inconsistently, resulting in progressive cracking that produced the bowing panel profile. In-house laboratory testing revealed that the marble had experienced a 40 percent reduction in strength and was forecast to lose an additional 30 percent over the next ten years. Additionally, WJE engineers utilized state-of-the-art methods, including 3D computer analysis, in situ load testing, and wind tunnel studies, to establish the maximum wind load pressures the panels were required to withstand. WJE found that the building experienced a wind load 20 percent greater than code required. Given the high wind demand and loss of strength, total recladding was the only viable solution. After an exhaustive search for white stone that closely resembled the original marble, WJE conducted a battery of accelerated weathering tests on each sample; full-scale mock-ups of the specimens that performed best were then subjected to wind and pressure tests. Based on the results, WJE engineers recommended white Mt. Airy granite to replace the marble. In addition to managing the extensive recladding project, WJE engineers designed and tested a stronger connection system for the new, thicker panels and reinforced many of the building's below-grade columns to accommodate their additional weight. WJE's project involvement significantly extended the facade's physical life and preserved the building's signature look.
RELATED INFORMATION
-
Clients turn to us when they need a firm that fully understands the aesthetic and functional... MORE >Services | Building Enclosures
-
Our materials scientists provide comprehensive consulting services for the evaluation and... MORE >Services | Materials Evaluation and Testing
-
Our professionals deliver practical repair and rehabilitation services that maximize the... MORE >Services | Repair and Rehabilitation